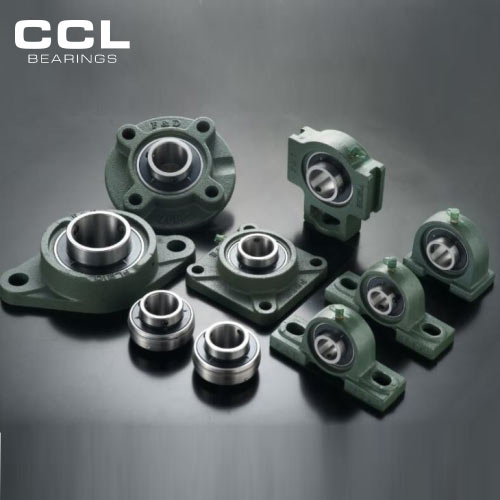
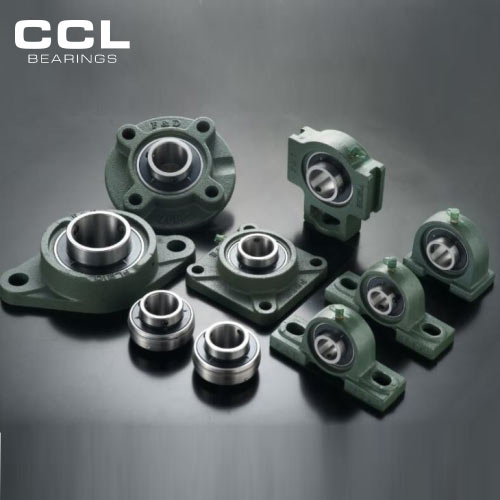
With a global impact of roughly $26 billion, handheld power tools are an essential tool for residential, industrial and commercial applications. As such, it’s important to recognize the role that ball bearings play in their performance; enduring combined loading conditions and high-speed operation; enabling low friction, low noise, and low vibration; and ensuring reliability. Below is a summary of the most important considerations when specifying or selecting ball bearings for handheld power tools.


Bearing loads: Ball bearings are an ideal component for power tools. They support both radial and axial loads simultaneously. If axial loads are excessive, supplement radial ball bearings with thrust bearings to effectively support these loads.
Noise and vibration: When power tools emit noise and vibration, it directly impacts the operator and results in fatigue and general dissatisfaction with the tool. Several factors may be at play, including bearing quality, poor tool design, or poor process control during manufacture and assembly of the tool.
Bearings with rings that have poor geometry tend to emit lower frequency noise and vibration, while balls or raceways with poor surface finishes tend to emit higher frequency noise and vibration. We recommend using bearings produced to Electric Motor Quality (EMQ) noise levels, which indicate their suitability for use in electric motors.
To minimize noise and vibration, manufacturers of power tools should properly specify and apply preload to the bearings. The application of axial preload forces the balls into contact with raceways, establishing a contact angle which causes the ball set to rotate in a uniform circumferential plane. Preload is critical in high-precision and high-speed power tool applications where speeds can reach 60,000 RPM.
Running temperature: To minimize the running temperature of power tools, manufacturers must mount bearings properly while having the appropriate preload and lubrication type.
Bearing materials: To optimize performance, bearings should be manufactured using high-quality materials. Bearings rings and balls are commonly produced using SAE 52100 chrome steel, which delivers excellent fatigue strength and wear resistance. If there is a risk of exposure to moisture, martensitic stainless steel should be used.
Ceramic balls offer additional high-speed benefits, though they are not typically used in handheld power tools.
Lubrication: Designers and engineers often overlook the importance of lubrication in the performance and life of ball bearings.
Typically, the bearings found in small power tools are lubricated once for the lifetime of the device. Operating temperature is the primary consideration when selecting a lubricant, with temperature directly impacting the base oil’s viscosity, which in turn impacts the ability to support loads.
Harsh environments: When power tools will be continuously exposed to liquids or debris, consider the use of seals or shields to protect the bearing.
Nitrile rubber is a common bearing seal material, providing protection from contamination, but reduces the maximum speed capability of the bearing. This is a design trade off that favors durability.
With multiple variables and factors that impact bearing performance in handheld tools, we recommend consulting a bearing applications specialist, who can assist with calculating load capacity, bearing life, fits and component tolerances.
———